اتصل
هاتف
+0086-371-86162511
عنوان
تشنغتشو ، الصين
impact crusher particles
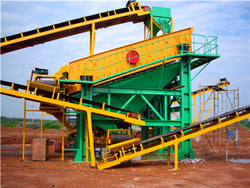
Modelling and simulation of particle breakage in impact
In impact crushers, the breakage probability depends mainly on the grain size and the kinetic impact energy ( King and Bourgeois, 1993 ), which is clearly a dynamic variable. Therefore, we have to define another, more suitable classification function that The DEM method, including a particle replacement breakage model, has been successfully demonstrated using a broad range of existing compression based Simulation of particle flows and breakage in crushers using DEM
احصل على السعر
The influence of particle shape on parameters of impact crushing
The sizing and design of the impact crushers are based on the feed parameters, such as the material to be crushed, the mass flow, diameter and moisture of In an impact crusher, all particles are subjected to impact and the elongated particles, having a lower strength due to their thinner cross section, would be broken (Ramos et al., 1994; Impact Crusher an overview ScienceDirect Topics
احصل على السعر
Modelling and simulation of particle breakage in impact crushers
The minimum size of the particles that undergo breakage is assumed to be a function of the impact energy and the feed rate. The model predictions are A number of experiments were conducted on a laboratory batch impact crusher to investigate the effects of particle size and impeller speed on grinding rate and product size distribution. The experiments Minerals Free Full-Text Milling Studies in an
احصل على السعر
(PDF) Modelling and simulation of particle
In this paper, we present a phenomenological model that predicts the size distribution of the product issued from impact crushing in function of the rotor strike radius and velocity, the material...The aim of this paper is to provide a foundation for systematic particle based modelling of crushers by applying a reasonably sophisticated DEM model to a wide Simulation of particle flows and breakage in crushers using
احصل على السعر
Simulation of particle flows and breakage in crushers using
The breakage method used is based on facture of particles using geometric rules for progeny generation and estimates of the force applied to the particles as they Equipment. In a high-speed rotary impact crusher, the arm of the rod, hammer, or board rotates at a high speed around a horizontal or vertical axis, producing impact collisions with particles [18, 19].This equipment for the size reduction of materials can also be called an impact grinder.An impact crushing dynamic model of waste printed circuit board particles
احصل على السعر
Impact Crusher an overview ScienceDirect Topics
A jaw crusher crushes only a small proportion of the original aggregate particles but an impact crusher crushes mortar and aggregate particles alike and thus generates a higher amount of fine material (O’Mahony, 1990). Gyratory crushers work on the same principle as cone crushers (Figure 4.4(c)). These have a gyratory motion driven by anIn general, there is a tendency of sphericity reduction (between 15 and 22%) with the reduction of particle sizes for cone crusher-generated aggregates. For the impact-produced aggregates, no clear tendency exists when it comes to sphericity variation. The B-I aggregate (from the impact crusher) presented slightly lower sphericity when The influence of crushing processes and mineralogy of aggregates
احصل على السعر
Production of Manufactured Sand SpringerLink
Producing of sand: some aggregates with a particle size of 5–40 mm and below 5 mm are sent to the vertical impact crusher for producing sand, and the fines content is adjusted by fines removal equipment. (7) Spray humidification: the MS is humidified by the spray system to prevent segregation.A number of experiments were conducted on a laboratory batch impact crusher to investigate the effects of particle size and impeller speed on grinding rate and product size distribution. The experiments involved feeding a fixed mass of particles through a funnel into the crusher up to four times, and monitoring the grinding achieved with each Minerals Free Full-Text Milling Studies in an Impact Crusher
احصل على السعر
Dust emission from crushing of hard rock aggregates
Crushing produces mainly coarse (TSP and PM 10) dust particles which settle near the dust source. The mass concentration of coarse particles varied from few tens of μg/m 3 to over 6 × 10 3 μg/m 3 downwind from the crusher. The mass concentration of fine particles (PM 2.5 and PM 1) ranged between ten μg/m 3 and few hundreds of μg/m 3Cleary and Sinnott and [9, 10] used DEM to simulate particle flow in the crusher and estimated the stress applied by particles flowing through the crusher. e study by da Cunha et al. [11] showed(PDF) Simulation of solids flow and energy transfer in a
احصل على السعر
Simulation of particle flows and breakage in crushers using DEM
The DEM method, including a particle replacement breakage model, has been successfully demonstrated using a broad range of existing compression based crushers. Predictions for five types of crushers: jaw crusher, cone crusher, gyratory crusher, impact crusher and double roll crusher were presented.Predictions for five types of crushers: jaw crusher, cone crusher, gyratory crusher, impact crusher and double roll crusher were presented. The breakage method used is based on facture of particles using geometric rules for progeny generation and estimates of the forces applied to the particles as they flow through the crusher. UnlikeSimulation of particle flows and breakage in crushers using
احصل على السعر
Simulation of solids flow and energy transfer in a vertical
Semantic Scholar extracted view of "Simulation of solids flow and energy transfer in a vertical shaft impact crusher using DEM" by E. R. Cunha et al. (DEM) is the most suitable modeling technique to simulate the mass flow of particles in chamber recently, which is an important part of VSI to break rock. DEM is presented Expand. 1.Mathematical simulations for breakage rate and breakage function of cone crusher [43] Stress: Compression, shear, attrition, impact, and internal forces: Mode of fragmentation: Abrasion, chipping and massive breakage: Product particle morphology studies of ball mill, jet mill, attrition mill, stirred bead mill [56] – Mode of breakageBreakage process of mineral processing comminution
احصل على السعر
Simulation and experimental study on the stone powder
At present, the main crushing equipment utilized in manufactured sand production is the cone crusher and the vertical shaft impact (VSI) crusher. The ability to limit the amount of stone powder produced is the major advantage of the cone crusher [1], [2], [3]. However, for most particle sizes, the fragment shape is poor [4].An impact crusher is rarely used with hard rock materials due to wearing. Commonly, an encapsulated sieve is adopted together with every crushing unit apart from the primary crusher. (PM 2.5 and PM 1) ranged between ten μg/m 3 and few hundreds of μg/m 3 downwind from the crusher. Fine particles originate mainly from the machinery Dust emission from crushing of hard rock aggregates
احصل على السعر
Simulation of solids flow and energy transfer in a vertical
In spite of its relative operational simplicity and earlier attempts to model its performance, the Vertical shaft impact (VSI) crusher is still lacking a comprehensive mathematical description that allows predicting its performance accurately. One of the reasons is the limited knowledge of particle interaction and solids flow inside the machine.The particle breakage in the VSI is achieved through rock against rock impact. This breakage mechanism is more random compared to the cone crusher, and there is a probability that some stones pass through the crusher unbroken. In addition, the impact breakage has been shown to produce more fine material than what is observed in a cone Energy considerations in compressive and impact crushing
احصل على السعر
US2844331A Impact crusher Google Patents
Patented July 22, 1958 Each bottom plate 15 is preferably of a relathe impact surface 26 is an involute about the circle 27 which, as stated, is of a diameter less than the diameter of a circle generated by the point of discharge of particles from the impeller. While a single impact surface 26, in the form of an involute about the circle 27, might be formed. in a With the valuable insights drawn from the foundational work done on systematic particle-based modelling for a wide range of crushers [3,5], this study focuses on the design factors that can improve the performance of an impact crusher. Using the DEM outputs such as spectral energy of inter-collisions and visual particle activity, the impact Numerical Simulation of a Single and Double-Rotor Impact Crusher
احصل على السعر
Simulating breakage tests using the discrete element
The Bond twin pendulum device has been modeled as two horizontal impactors that hit each individual particle at impact energies given by Eq. . Simulating a laboratory-scale cone crusher in DEM using polyhedral particles. Powder Tech 372:362–371. Article Google Scholar Mahmoud E, Papagiannakis AT, Renteria D (2016) Fladvad and Onnela [] studied the influence of jaw crusher parameters on the quality of primary crushed aggregates.In the hammer crusher (Figure 2), hammerheads of high wear resistance and strength are attached to the tip of a rotor placed inside a well-sealed, noiseless, and fixed casing.As the hammerheads rotate with a high speed, they Finite Element and Multibody Dynamics Analysis of a Ball Mill Glass Crusher
احصل على السعر- مطحنة ريموند توفير الطاقة وحماية البيئة
- satara maharashtra nagewadi om siddhi stone crushers
- التعدين الرمال السيليكا مستعملة
- الحب آلة طحن من روسيا
- قدرة كسارة المطرقة كسارة
- contoh business plan coal mining company
- تكلفة آلة طحن التجارية في بنغالور
- مصنع طاحونة كسارة
- معدات إنتاج الفحم البني
- bowl feeder vibrator shinko crusher usa
- المورد الخرسانة سحقت
- نوع الفك الحجر تستخدم مصغرة الفك محطم
- آلة لمناجم الذهب معدات تعدين الذهب المحمول
- bond mill work index definicion
- تأثير آلة كسارة الفحم