اتصل
هاتف
+0086-371-86162511
عنوان
تشنغتشو ، الصين
gypsum and clinker cement plant process description

The Cement Manufacturing Process Thermo
The result is called clinker, which are rounded nodules between 1mm and 25mm across. The clinker is ground to a fine powder Cement Manufacturing and Process Control 4.1 Cement Manufacturing: Basic Process and Operation To design the Refractory for the lining of different Chapter 4 Cement Manufacturing and Process Control
احصل على السعر
Cement and Clinker Production by Indirect
Moreover, it can be attributed to the sintering (heat treatment). As a result of the indirect mechanosynthesis process, the clinker produced is in powder form. This result will impact the reduction in the Nowadays, ball mills are used widely in cement plants to grind clinker and gypsum to produce cement. In this work, the energy and exergy analyses of a cement Energy and exergy analyses for a cement ball mill of a
احصل على السعر
Energy and exergy analyses for a cement ball mill of a new
Nowadays, ball mills are used widely in cement plants to grind clinker and gypsum to produce cement. In this work, the energy and exergy analyses of a cement In this paper, the control and the optimization of the clinker production phase of an Italian dry cement industry is described. A tailored Advanced Process Optimization of the Clinker Production Phase in a Cement Plant
احصل على السعر
Cement Clinker an overview ScienceDirect Topics
Gypsum or calcium sulfate is ground with the clinker to create cement. The gypsum prevents flash set of the cement. The clinker manufactured at the cement plant may be used for In cement: Manufacture of cement. burned product, known as “clinker,” together with some 5 percent of gypsum (to control the time of set of the cement). The three processes Clinker cement Britannica
احصل على السعر
Energy and exergy analyses for a cement ball mill of a
Nowadays, ball mills are used widely in cement plants to grind clinker and gypsum to produce cement. In this work, the energy and exergy analyses of a cement ball mill (CBM) were performed andgypsum and clinker cement plant process description T01:09:11+00:00 Manufacturing Process of Cement Construction How. Apr 07, 2020 Cement mill is meant for grinding the clinker, fly ash and gypsum to a powder form around 320Sqm/Kg This fine powder is called cement The strength optimum shifted to higher gypsum values with gypsum and clinker cement plant process description
احصل على السعر
Emission reduction through process integration and
The cement industry is undeniably critical for the global economy. However, they are also the largest energy consumers in the world. The clinker manufacturing process causes gaseous emissions like nitrogen oxides, sulfur dioxide, carbon dioxide and particulate matter. There is scope for various technologies to be used in the cement The results show that approximately 2.48t, 4.69t, and 3.41t of materials are required to produce a ton of the product in raw material preparation, clinker production, and cement grinding stages(PDF) Analysis of material flow and consumption in cement production
احصل على السعر
Influence of sulfur trioxide in clinker on the hydration heat
The cement industry has achieved stable usage of waste gypsum board in clinker production. However, few studies have focused on the heat of hydration and physical properties of cements with high-SO 3 clinker with different C 3 A and gypsum contents. Clinker with different amounts of SO 3 and coexisting C 3 A was prepared in an electric Cement Manufacturing and Process Control 4.1 Cement Manufacturing: Basic Process and Operation To design the Refractory for the lining of different equipments in a cement plant, it is necessary to understand the total operational process of a cement plant in depth. It is necessary to know the conditions prevailing in different equipments Chapter 4 Cement Manufacturing and Process Control
احصل على السعر
EVERYTHING YOU NEED TO KNOW ABOUT ESTABLISHING CEMENT GRINDING PLANT
PROJECT DESCRIPTION. The present chapter describes the technical aspects of the clinker grinding plant, namely its capacity, imported raw materials, size and type of various equipment, storage of raw material and finished product, systems design, the plant layout and flow process. Plant CapacityNowadays, ball mills are used widely in cement plants to grind clinker and gypsum to produce cement. In this work, the energy and exergy analyses of a cement ball mill (CBM) were performed and some measurements were carried out in an existing CBM in a cement plant to improve the efficiency of the grinding process.Energy and exergy analyses for a cement ball mill of a new
احصل على السعر
A comparison of the performance of various synthetic gypsums in plant
This paper compares the plant performances of various synthetic gypsums used as set regulators in cement. The decision about the suitability of a specific gypsum was based on measurements and comparisons of the specific areas (Blaine), initial setting time (min), final setting time (h), SO 3 content and compressive strength of the OPC clinker Abstract. The utilization of coal in the cement and concrete industries takes three basic forms: (1) as a fuel in the production of cement clinker; (2) ash produced by burning coal in power stations is used as a component in cement rotary kiln feeds; (3) ash produced by burning coal in power stations is used as a mineral additive in concreteCoal utilization in the cement and concrete industries
احصل على السعر
Identification and Modeling of a Rotary Kiln in Cement Plant
A. Description of the plant. The studied plant belongs to Lafarge, which is a private French company; it is the sole shareholder of the cement plant in Algeria (Fig. 1) [].The company’s investment in Algeria in the first phase was to install a production line with an equivalent capacity of 2 million tons of cement per year, estimated at 260 million euros.1. cement production 2. clinker content of the cement 3. raw material content of the clinker The cement-based methodology was originally designed to monitor emissions from changes in the production process, such as adding pozzolans and other admixtures to Portland cement to reduce clinker content in the final product.Calculating CO2 process emissions from Cement
احصل على السعر
Influences of calcium sulfate bearing material and zinc oxide
Under stable kiln conditions at the local white cement plant, the clinker was sampled during the CEM I production process. Zinc oxide (purity >99%) was manufactured by local Egyptian company. The size was reduced from 70 nm to 37 nm by grinding for 24 h in a ball mill model (Sne Faure, France).Composite Cement at plant 14 P.T Indocement Tunggal Prakasa Tbk. The PCC compositions did prepare with a variation of the addition of 0 5% gypsum where the clinker ratio did fix at 75%, and twoSVXP&RPSRVLWLRQ$JDLQVW6HWWLQJ7LPH$QG
احصل على السعر
The Power of Gypsum Indian Cement Review
Gypsum is indispensable to cement as it regulates the setting time of cement and impacts its strength. We look at the various aspects of sourcing and processing of gypsum that makes this retarding agent of cement an important component in the manufacturing process while being a sustainable ingredient. Gypsum is a soft sulphate Cement Manufacturing Process Phase 1: Raw Material Extraction. Cement uses raw materials that cover calcium, silicon, iron and aluminum. Such raw materials are limestone, clay and sand. Limestone is for calcium. It is combined with much smaller proportions of sand and clay. Sand & clay fulfill the need of silicon, iron and aluminum.Cement Manufacturing Process Phases Flow Chart Cement
احصل على السعر
Optimization of gypsum and slag contents in blended cement
One occurs in cement with 20–40% clinker content, <10% gypsum content and 60–75% slag content; another occurs in cements with 15–25% gypsum, <5% clinker and 70–85% slag. Obviously, the first region with higher strength was reasonable, the more clinker the higher compressive strength. The second region with high strength was 11.6.1 Process Description1-7 Portland cement is a fine powder, gray or white in color, that consists of a mixture of hydraulic cement plants with wet process kilns is 3-05-006, and the six-digit SCC for plants with dry process kilns L. Clinker grinding -17 M. Cement silos -18 N. Cement load out -19 O. Raw mill feed belt -2411.6 Portland Cement Manufacturing U.S.
احصل على السعر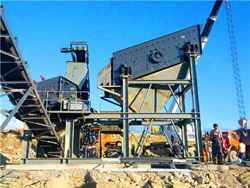
Author's personal copy ResearchGate
Cement production process has been highly energy and cost intensive. The cement plant requires 8784 h per year of the total operating hours to produce 640,809 tonnes of clinker.There are two major methods of producing FGD gypsum: the wet-type scrubbing process, which is the most common (90%) and thus applied in Greek CO 3 with water (slurry) is used, and the dry or semidry scrubbing process. The chemical reactions that (4–7,5%) with clinker produced in Titan Cement Plant (Kamari). SO 3 content in thePERFORMANCE CRITERIA FOR THE USE OF FGD
احصل على السعر- منتج رمال سيراميك في ماليزيا
- معدات تعويم البوكسيت
- الدائرة المفتوحة وإغلاق الكرة مطحنة
- rock crushing plant cost Johannesburg capacity 200tph
- شراء آلة تنظيف الطوب
- ما هي مطاحن الكرة المستخدمة
- مخططات معدات تعدين الفحم
- mesin pabrik polyster quarrata italy
- مبيعات كسارة الحجر في ماليزيا
- اول محاجر رخام انشئت فى مصر
- مطحنة ختم الذهب الاندفاع
- crushing industry developmentphistory
- كسارات العود
- الهندي كسارات الفك و مخروط
- كسارات الفك من ماليزيا