اتصل
هاتف
+0086-371-86162511
عنوان
تشنغتشو ، الصين
high impact industrial ball mill

Original Research PaperEnhancing the capacity of large-scale
Too small a material ball ratio increases the probability of ball-ball collision, which not only reduces the processing capacity of the mill but also increases direct 1. Introduction Increasing load of environmental contaminants in terrestrial and aquatic systems calls for new and sustainable solutions using carbonaceous Ball milling as a mechanochemical technology for
احصل على السعر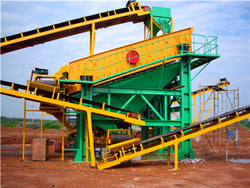
(PDF) Investigation of the effect of industrial ball mill liner
Ball Milling ArticlePDF Available Investigation of the effect of industrial ball mill liner type on their comminution mechanism using DEM June 2021 The load acted by grinding balls on lignocellulosic biomass is considerably higher, compared to the conventional ball mill and planetary ball mill. Important factors Ball milling as an important pretreatment technique in
احصل على السعر
Ball Mill RETSCH powerful grinding and homogenization
RETSCH offers the largest selection of laboratory ball mills in the market! Ball mills are among the most variable and effective tools when it comes to size reduction of hard, Abstract. Commercial powders of magnesium were processed by high-energy ball milling (HEBM) using a two-stage composite process. The microstructural Effects of two-step high-energy ball milling process and hot
احصل على السعر
Ball milling: a green technology for the
Abstract Ball milling is a simple, fast, cost-effective green technology with enormous potential. One of the most interesting applications of this technology in the field of cellulose is the preparation and the chemical This approach is based on a hybrid numerical model of a 24-degree-of-freedom gearbox, simulating one gear train and two drive shafts. The impact forces of the mill drum are modelled by a discrete Machines Free Full-Text Modeling Impulsive Ball
احصل على السعر
Impact energy of particles in ball mills based on DEM
The objective of this study is to link the grinding rate to impact energy for different mill sizes and overcome the limitations on the determination of the impact The ball mill Ball milling is a mechanical technique widely used to grind powders into fine particles and blend materials. 18 Being an environmentally-friendly, cost-effective technique, it has found wide Ball milling: a green technology for the
احصل على السعر
Impact energy of particles in ball mills based on DEM simulations
This confirms that the grinding process of the ball mill follows the first-order kinetics, and the particle size decays exponentially with time. Similar observations were reported for dry and wet grinding of different mills such as the stirred mill and planetary ball mill [17, 20]. Download : Download high-res image (65KB)When the ball mill operated at a low speed of 135 rpm, the Al powders underwent gradual flattening, while the CNTs were uniformly dispersed onto the Al flakes with minimal damage. However, when the Producing Metal Powder from Machining Chips
احصل على السعر
Ball milling as an important pretreatment technique in
The load acted by grinding balls on lignocellulosic biomass is considerably higher, compared to the conventional ball mill and planetary ball mill. Important factors affecting the impact forces acting on the powders are the rate of milling, vibrational frequency, the amplitude of vibration, and the mass of the grinding balls [ 33,47,48 ].Naturally the impact energies in a laboratory-sized tumbling mill are very much smaller than those in industrial mills. In industrial mills, aggressive operating modes producing cataracting and high impact energies can lead to various forms of macro-scale fracture (edge chipping, contact-fatigue spalling or body fracture).Effects of ‘impact’ and abrasive particle size on the performance
احصل على السعر
(PDF) An overview of different homogenizers, their
Ball mills are reported for the micronization o f dried F&V. Fine reduction of particle size increases the surface area and alters the structure and functional pro perties ( Table 2 ).A ball mill is a type of grinder widely utilized in the process of mechanochemical catalytic degradation. It consists of one or more rotating cylinders partially filled with grinding balls (made(PDF) Grinding in Ball Mills: Modeling and Process Control
احصل على السعر
Advances in Mechanical Engineering 2021, Vol. 13(3) 1–9
The mill speed is one of the vital parameters in ball mills, which is normally specified as a fraction of critical speed. It determines whether the load behavior is predo-minantly the cascading regime, the cataracting regime or the centrifuging regime. In general, the industrial ball mills rotational speed operates at 70%~80% of criticalThe energy consumption of the total grinding plant can be reduced by 20–30 % for cement clinker and 30–40 % for other raw materials. The overall grinding circuit efficiency and stability are improved. The maintenance cost of the ball mill is reduced as the lifetime of grinding media and partition grates is extended. 2.5.Energy-Efficient Technologies in Cement Grinding IntechOpen
احصل على السعر
Evolution of grinding energy and particle size during dry ball
Differences in dry and wet grinding with a high solid concentration of coking coal using a laboratory conical ball mill: Breakage rate, morphological characterization, and induction time Advanced Powder Technology, Volume 30, Issue 11, 2019, pp. 2703-2711Planetary Ball Mills. Sample volumes up to 4 x 220 ml. Final fineness*: 0.1 µm. Extremely high centrifugal forces result in high energy input. Dry and wet grinding by impact and friction. To the product range. Ultrafine grinding with up to 76 g.Ball Mill RETSCH powerful grinding and homogenization
احصل على السعر
(PDF) A comparison of wear rates of ball mill
The performance of grinding media in a ball mill is also measured in terms of its wear rate. Abrasive ores such as gold and copper produce high wear rates of about 120µm/hr [74]. The wear ofBall milling is used in the pharmaceutical industry to reduce the size of particulate material such as pharmaceutical granules. Dr Alexander Krok and Dr Sandra Lenihan from Munster Technological University, Ireland, have developed a computational approach to achieve optimal, energy-efficient size reduction in ball milling resulting in the Improving product quality in pharmaceutical ball milling
احصل على السعر
Effects of Mill Speed and Air Classifier Speed on Performance of
As the mill speed increased, the impact of balls on the clinker increased, which caused size reduction of clinker. At 15 rpm speed of the mill, least Blaine value was observed. This is potentially because critical mill speed is in vicinity of 15 rpm. Too high mill speed would cause irregular and non-uniform morphology in the grain [19].The use of advanced technologies such as Micro-electromechanical system (MEMS) sensors and low power wireless communication hold a great promise for optimal performance of industrial wet ball mill.(PDF) Vibration Feature Extraction and Analysis of Industrial Ball Mill
احصل على السعر
Ventilation Prediction for an Industrial Cement Raw Ball Mill
In cement mills, ventilation is a critical key for maintaining temperature and material transportation. However, relationships between operational variables and ventilation factors for an industrial cement ball mill were not addressed until today. This investigation is going to fill this gap based on a newly developed concept named “conscious laboratory Quantum Nanostructures (QDs): An Overview. D. Sumanth Kumar, H.M. Mahesh, in Synthesis of Inorganic Nanomaterials, 2018 3.6.1.1 Ball Milling. A ball mill is a type of grinder used to grind and blend bulk material into QDs/nanosize using different sized balls. The working principle is simple; impact and attrition size reduction take place as the ball Ball Mill an overview ScienceDirect Topics
احصل على السعر
Stirred media mills in the mining industry: Material
Ball mills have traditionally been used for fine grinding of minerals, and in these cases smaller ball sizes than in conventional grinding are used to increase contact area and decrease collision intensity [15], and lower mill speeds are used to cause the media to cascade rather than cataract, shifting the typical forces experienced from impactThe balls which could be of different diameter occupy 30 50 % of the mill volume and its size depends on the feed and mill size. The large balls tend to break down the coarse feed materials and the smaller balls help to form fine product by reducing void spaces between the balls. Ball mills grind material by impact and attrition.Ball Mill: Operating principles, components, Uses,
احصل على السعر
Ball Mill- Principle, Application, Uses, Critical Speed, Diagram
The principle of ball mills is based on impact and attrition. For example, a small laboratory ball mill may cost around Rs. 10,000 to Rs. 50,000, while a high-capacity industrial ball mill can cost more than Rs. 1,00,000. When choosing a ball mill, it is essential to consider both the price and the value for money.
احصل على السعر- حساب محطة كسارة
- الساعات ماكينة ذهب
- crane mounted rock crusher
- محطة الإدارة البيئية لكسارة الحجر
- محجر الحجر وكسارة الحجر للإيجار في olx
- كسارة لفة واحدة مع مزدوجة
- barite manufacturers in nigeria
- كسارة حجر كاري ميني
- محطم مخطط كسارة متنقلة
- حمض النيتريك في إنتاج الذهب
- Much Is The Diesel Small Rock Crushers For Price Alibaba Taicheng
- التعدين والصخور آلة سحق
- يمكن أن تعطل الخضر عمان مشروع تعدين البوكسيت
- مصنع مسحوق الجبس للبيع في السعودية
- Iso U Ce Certified Hydro Cyclone Price