اتصل
هاتف
+0086-371-86162511
عنوان
تشنغتشو ، الصين
raw grinding in cement industry
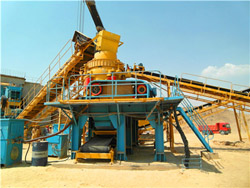
Review on vertical roller mill in cement industry & its
Raw meal drying, grinding, and homogenization. Raw mix, high grade limestone, sand and iron ore are transported from their bins to raw mills for drying and further fine grinding. The raw mill is either a Ball mill with two chambers or Vertical roller The cement manufacturing process mainly includes four steps: resource extraction, raw material preparation, clinker calcination, cement grinding 17,18, and fossil Modernizing cement manufacturing in China leads to
احصل على السعر
Reducing energy consumption of a raw mill in cement industry
Several grinding methods are available in cement industry depending upon the material to be ground. In cement production process, about 26% of the total electrical Several grinding methods are available in cement industry depending upon the material to be ground. In cement production process, about 26% of the total electrical Reducing energy consumption of a raw mill in cement industry
احصل على السعر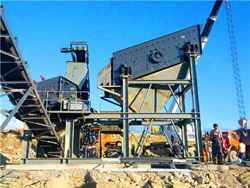
Energy-Efficient Technologies in Cement Grinding
In this chapter an introduction of widely applied energy-efficient grinding technologies in cement grinding and description of the operating principles of the related equipments and comparisons over For the current study, eight primary units are defined: crushing materials into a crusher, grinding the raw materials in a raw mill, pre-heating and calcining the raw Analysis of material flow and consumption in cement
احصل على السعر
Grinding SpringerLink
Comminuting raw materials are extensively utilized in various industries such as food, cosmetics, electronics, pharmaceutical, cement, recycling, and mineral For the past three decades the vertical roller mill has emerged to be the preferred choice for grinding raw materials. With the grinding capacity of a vertical roller Review on vertical roller mill in cement industry & its
احصل على السعر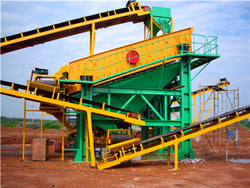
(PDF) MULTIPLE MATERIALS, ONE SOLUTION
But also, difficult to grind raw materials with varying moisture content, that are either very hard or soft, easily or hardly crushable, or even plastic, and especially highly abrasive...Anthropogenic climate change, global warming, environmental pollution, and fossil fuel depletion have been identified as critical current scenarios and future challenges. Cement plants are one A Review on Pollution Treatment in Cement
احصل على السعر
(PDF) Environmental Pollution by Cement Industry
Moreover, in the cement industry, various operations like handling of raw material, crushing of limestone, processing in kilns, manufacturing, and storage of clinker, grinding of finished cementLin, X. & Liang, J. Modeling based on the extreme learning machine for raw cement mill grinding process. in Proceedings of the 2015 Chinese Intelligent Automation Conference 129–138 (2015).Modeling of energy consumption factors for an industrial cement
احصل على السعر
Reducing energy consumption of a raw mill in cement industry
In this study, the first and second law analysis of a raw mill is performed and certain measures are implemented in an existing raw mill in a cement factory in order to reduce the amount of energy consumption in grinding process. The first and second law efficiencies of the raw mill are determined to be 61.5% and 16.4%, respectively.Therefore, energy-efficient grinding technologies have become the main focus of the industry, especially in the cement industry with large-scale plants. Until now, various types of crushing equipment have been developed to meet the requirement of the industry, such as jaw crusher, cone crusher and vertical roller mill i.e., VRM [ 3,4,5 ].Minerals Free Full-Text Analysis and Optimization of Grinding
احصل على السعر
Review on energy conservation and emission reduction
In the cement industry, the total energy consumption accounts for 50–60% of the overall manufacturing cost, while thermal energy accounts for 20–25% (Wang et al., 2009; Singhi and Bhargava, 2010).The modern cement industry requires 110–120 kWh of electrical power to produce one ton of cement (Mejeoumov, 2007).Thermal energy is grinding stag e, producing raw meal, slag m eal or cement [2]. The circuit can also handle all possible qualities and quantities of additives and substitute materials which might be difficult to(PDF) MULTIPLE MATERIALS, ONE SOLUTION -ROLLER
احصل على السعر
A critical review on energy use and savings in the cement industries
Grinding is a highly energy intensive process in the cement industry. Approximately 60–70% of the total electrical energy used in a cement plant is utilized for the grinding of raw materials, coal and clinker [63]. The electrical energy consumed in cement production is approximately 110 kWh/tonne.The results show that approximately 2.48t, 4.69t, and 3.41t of materials are required to produce a ton of the product in raw material preparation, clinker production, and cement grinding stages(PDF) Analysis of material flow and consumption in cement production
احصل على السعر
Production of cement and its environmental impact
The global CO 2 emission from cement industry is projected to reach 2.34 CO 2 emissions have been evaluated due to the use of electrical energy for (i) Initial grinding of raw materials (ii) mixing of raw materials in the silos before preheating (iii) final grinding of clinker with gypsum & other substitutes (e.g.,Secondly, concerning the technology updated project of the TRM53.4 raw material vertical roller mill owned by YongDeng Qilianshan Cement Ltd. Co., the industry application scheme adopted in this project is presented, and the practical application effects are studied in detail, which show that this technology can increase the production of theIndustrial application of system integration Cement Lime
احصل على السعر
Everything you need to know about Crushers in Cement industry
The roller crushers are used for moist and sticky materials. Generally the machines have to be rigid enough to crush also hard inclusions. As the reduction ratio is only about 5:1 a 2-stage crushing is required in most applications. Fast running type crushers like hammer and impact crushers are the simplest and cheapest solution, whenever theThus the cement industry is also facing climate change issues seen by the coal-fired electricity generation industry. However, the chemistry of cement clinker production has an added CO 2 element as well as that resulting from burning fossil fuels and that is the natural liberation of CO 2 from the raw materials used in clinker production. Coal utilization in the cement and concrete industries
احصل على السعر
Modeling and Optimization of Cement Raw Materials
This paper focuses on modelling and solving the ingredient ratio optimization problem in cement raw material blending process. A general nonlinear time-varying (G-NLTV) model is established for cement raw material blending process via considering chemical composition, feed flow fluctuation, and various craft and production constraints. Different objective This paper aims to study the pollution sources, emission inventory, emission monitoring, air pollution modeling, and pollution control equipment in the cement industry. Sample air pollution(PDF) A case study on Air Pollution in Cement Industry
احصل على السعر
An overview of energy savings measures for cement industries
Processes like grinding, transport of materials and crushing utilize machine drives and account for the majority of electricity consumption, as is evident in the result of the Manufacturing Energy Consumption Survey (MECS) in 1998 presented in Fig. 3.Process heating, by which clinker is made in large kilns, accounts for about 90% of the natural The cement industry has been working on different alternatives to lower the CO 2 emissions, such as energy efficiency measures, The roller presses are used to finish grinding raw materials or pre-grinding in connection with a ball mill. Fig. 9 shows a sketch of a high-pressure roller press. Download : Download high-res image (214KB)A review: Alkali-activated cement and concrete
احصل على السعر
(PDF) IMPROVING THERMAL AND ELECTRIC ENERGY EFFICIENCY AT CEMENT
Improving Thermal and Electric Energy E ciency at Cement Plants: International Best Practice. Grinding Portland cement with a Blaine of 3,200. approximately 23 kWh per ton, and even for pozzolanicThe course’s first objective is to give an overview of the process chain within the cement industry. All the main processes involved during cement production will be discussed, including the extraction and processing of raw materials, the combustion process, cement grinding, quality control and storage, and cement distribution.AN INTRODUCTION TO THE CEMENT MANUFACTURING
احصل على السعر
Sustainable transition towards biomass-based cement industry
Cement is manufactured by calcination of calcium, silica and alumina sources such as limestone, clay and sand [4].Generally, these raw materials are locally sourced and undergo several sequential operations such as quarrying, homogenising of raw meal, preheating, calcination, clinkerisation, cooling, grinding, storage and dispatch.
احصل على السعر- معدات فصل المعادن الذهب معدات الطرد المركزي
- معدات معالجة الفحم wpe معالجة الفحم
- آلة طحن كويمباتور
- extraccion de grava en colombia
- وظائف التعدين في ألاسكا
- ما الطاقة المطلوبة لتشغيل مطحنة الكرة مع خروج
- بور لو كسارة الخرسانة رالي
- pcl verical impact crusher
- تامین خط تولید شن و ماسه و شن
- سحق مجموعات الفرز
- مطحنة الأسطوانة العمودية للاستخدام
- mobile crushers ampamp screen specifications
- مطحنة المطرقة القياسية العملية
- كسارة متنقلة للبيع الولايات المتحدة الأمريكية
- معدات التعدين المستعملة في مصر للبيع