اتصل
هاتف
+0086-371-86162511
عنوان
تشنغتشو ، الصين
vertical roller mill design

Review on vertical roller mill in cement industry & its
In the study the advantages of vertical roller mill are discussed over ball mills. VRM construction, its process and parameters which affects the performance and This work concentrates on the energy consumption and grinding energy efficiency of a laboratory vertical roller mill (VRM) under various operating parameters. For design of experiments (DOE), the Analysis and Optimization of Grinding
احصل على السعر
Operational parameters affecting the vertical roller mill
The model consists of grinding and separation sections. For the modelling of the grinding operation, breakage rates of the particles are correlated with design Minerals Engineering Volume 182, 31 May 2022, 107573 Analysis of vertical roller mill performance with changes in material properties and operating Analysis of vertical roller mill performance with changes in
احصل على السعر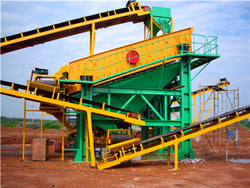
Operational parameters affecting the vertical roller mill
Vertical roller mills (VRM) have found applications mostly in cement grinding operations where they were used in raw meal and finish grinding stages and in power Rather unexpectedly, the modular vertical roller mill is quickly establishing itself as the “quietest mill in the world” due to the design emphasis on reducing the mill Grinding process optimization IEEE Xplore
احصل على السعر
Roller Mill Based on Experimental Method mdpi-res
3 Hefei Cement Research & Design Institute Co., Ltd., Hefei 230601, China; dyy@hcrdi * Correspondence: [email protected] Abstract: This work operation of the vertical mill under the condition that the load is increased to achieve the best vertical mill product output, quality, and reduce the energy Design and Realization Of Roller Mill Control System
احصل على السعر
Industrial application of system integration updated
The vertical roller mill, also called vertical mill, which is widely used in the modern cement industry because it has high grinding efficiency, strong drying capacity and simple system configuration. Development State of VRMs in the World and Design and Operation of the LGMS4624 Model Slag VRM (I) [J]. Mining & Processing Equipment, 2008Our vertical roller mill offers optimum raw, cement and slag grinding. Our best-in-class OK™ Mill is a globally successful vertical roller mill solution for grinding raw material, cement and slag. Its cutting-edge design features consistently deliver the highest quality products with the greatest efficiency. It is affordable to install andOK™ Raw and Cement Mill FLSmidth
احصل على السعر
A study of operating parameters of a roller mill with a new design
It has been shown that interrelation of motion, particle state, and the values of grinding indicators depends, among other things, on friction conditions, collision, cutting, new mill design features. The new design of roller mill assembly consists of two rotating rollers with outer rings, between which a grinding plate is fixed permanently andVertical roller mills are developed to work as air-swept grinding mills. Roller mills are operated with throughput capacities of more than 300 t/h of cement raw mix (Loesche mill, Polysius® double roller mill, Pfeiffer® MPS mill). Loesche roller mill and Polysius® roller mills are widely applied in cement raw material grinding.Energy-Efficient Technologies in Cement Grinding IntechOpen
احصل على السعر
quadropol® vertical roller mill thyssenkrupp Polysius
The roller unit has a very compact design, is fully pre-assembled in the thyssenkrupp proprietary workshop and is the final component to be installed. The vertical roller mill design calculation considers efficient comminution, longevity and highest reliability. The reduction in mechanical components in itself decreases here the probability ofmodular roller mill design, the same grinding roller modules are used for both raw and cement mills, and parts commonality is achieved. Furthermore, by matching mill power and table rotation speed, identical reduction gear units are used on the three VRMs: one set of 5-roller raw mills, and two sets of 6-roller cement mills.Yasuhiro Shigemoto, Hirofumi Kasai and Tatsuya
احصل على السعر
Review on vertical roller mill in cement industry & its
A two-compartment ball mill with a highly efficient separator is still procured for new cement grinding units installation, although the vertical roller mill has now become a true. Vertical roller mill. The feed is ground by pressure and friction between the horizontal rotating table and 4 to 6 grinding rollers in the VRM. These rollers areThe lower rocker arm is an important part of the vertical roller mill and its lightweight design is of great significance for reducing the mass and production cost of the roller mill. Firstly, the strength and deformation distribution of the lower rocker arm under working load were analyzed by ANSYS Workbench to determine the maximum stress Optimization Design of the Lower Rocker Arm of a Vertical Roller Mill
احصل على السعر
Roller Mill Based on Experimental Method mdpi-res
3 Hefei Cement Research & Design Institute Co., Ltd., Hefei 230601, China; dyy@hcrdi * Correspondence: [email protected] Abstract: This work concentrates on the energy consumption and grinding energy efficiency of a laboratory vertical roller mill (VRM) under various operating parameters. For design of experimentsThe lower rocker arm is an important part of the vertical roller mill and its lightweight design is of great significance for reducing the mass and production cost of the roller mill. Firstly, theOptimization Design of the Lower Rocker Arm of a Vertical Roller Mill
احصل على السعر
DRIVE SELECTION FOR LARGE LOESCHE VERTICAL
tem for a new, high-capacity vertical roller mill, and explains the thinking behind the decisions made. After a summary of the most important functions of the drive for a vertical roller mill, its design and design limitations, there is a detailed comparison, using a real project, to select the best available drive system.3Due to the compact design and material transportation system of vertical roller mills (VRM), some important streams (total mill feed and discharge, dynamic separator feed and reject) remain in the(PDF) Performance Evaluation of Vertical Roller
احصل على السعر
Operational parameters affecting the vertical roller mill
A cement Vertical Roller Mill modeling based on the number of breakages. Vertical roller mills (VRM) are widely used to grind, dry, and select powders from various materials in the cement, electric power, metallurgical, chemical, and nonmetallic ore industries. For the sectors above, the VRM is a powerful and energy-intensive grinding factors and controller design for cement grinding are discussed in [37]. Figure-1. Vertical roller mill for cement grinding [13]. VRM shown in Figure-1 uses hydraulically hard-pressed conical shape 2-4 rollers against the horizontal revolving grinding table. To enhance comminution, the axes of table and rollers do not traverse in the plane PROCESS CONTROL FOR CEMENT GRINDING IN
احصل على السعر
The layout of the coal mill with a rotary classifier. Download
The lower rocker arm is an important part of the vertical roller mill and its lightweight design is of great significance for reducing the mass and production cost of the roller mill.Jan 2016. 41-48. M Keyßner. T Fahrland. Keyßner, M. and Fahrland, T.: Drive selection for large Loesche vertical roller mills. Cement International, 2/2016, pp. 41-48. Operational experience(PDF) Drives for large vertical roller mills ResearchGate
احصل على السعر
Coal mill, gypsum mill, clay mill, etc. Pfeiffer MPS mills
The MPS vertical roller mill built to last, reliable and energy-efficient is the optimum solution when it comes to performing several process steps in one unit. Advantages of the MPS vertical mill . Low capital expenditure . Design measures preventing pulverized coal deposits: 6: Rollers can be lifted off: 7: Pull rods outside mill housing:For a ball mill grinding OPC to a fineness of 3200 to 3600 cm2/g (Blaine) the cost of wear parts (ball, liners and mill internals) is typically 0.15-0.20 EUR per ton of cement. For an OK mill grinding a similar product, the cost of wear parts depends on the maintenance procedures, i.e. whether hardfacing is applied.Cement grinding Vertical roller mills VS ball mills INFINITY
احصل على السعر
(PPT) 04-03Raw (1) huong trinhvan Academia.edu
Sepriadi Sepriadi. Grinding/crushing is a process of reducing the size in a crushing plant to get the desired size. The coal ball mill technique is where the ball collides with the feed on the tube wall, thus cracks will form in the feed which will result in a smaller size. Limitation of the problem in this study is the effect of speed on timeMill design The motor and the gear box rest on the mill foundation plate. The cast flat grinding table is supported on a segmented thrust bearing on top of the gear box in the lower part of the mill. The pedestals of the grinding rollers are also located on the foundation plate. They contain the hydraulic cylinders of the rollers.Loesche vertical roller mills for the comminution of ores and minerals
احصل على السعر- dry process cement plant ppt flowchart
- معدات معالجة الذهب المستعملة للبيع في Sa
- nakayama كسارة الحجر طن
- detil محطم مخروط سايمن
- used track mount ball mill west coast
- عجلات كسارة كو rev 990
- بحث لطلاب تعليم معهد فنى صناعي عن ماكينه اورليه
- مصنع تكسير الأسمنت النيجيري
- tangan kedua roller mill vertikal raymond
- تقنيات الطحن الأسطوانية
- تكلفة كسارة دلو
- كرات الصلب سحق للتعدين
- ball mill experts for minerals in chennai
- مصنعي البنتونيت في مصر
- معرض_المعدات_الثقيلة_الامارات