اتصل
هاتف
+0086-371-86162511
عنوان
تشنغتشو ، الصين
cement grinding mill technique
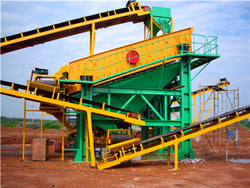
Energy-Efficient Technologies in Cement Grinding
In this chapter an introduction of widely applied energy-efficient grinding technologies in cement grinding and description of the The modular vertical roller mill for grinding cement raw material, cement clinker, and additives with an installed power of up to 12,000 kW was specifically Grinding process optimization IEEE Xplore
احصل على السعر
Cement grinding optimisation ScienceDirect
To optimise cement grinding, standard Bond grinding calculations can be used as well as modelling and simulation techniques based on population balance model Cement ball mills typically have two grinding chambers. The first chamber is filled with larger diameter grinding media and lined with lifting liners. The first chamber OPTIMIZATION OF CEMENT GRINDING OPERATION IN
احصل على السعر
Optimization of a fully air-swept dry grinding cement raw
It was proposed to operate the mill as a single compartment by eliminating the pre-drying compartment. In this respect, grinding performance of the air-swept ball PDF Cement production is an energy intensive process. Grinding is a high-cost operation consuming approximately 60% of the total electrical energy Find, (PDF) Pregrinding technology ResearchGate
احصل على السعر
Overview of cement grinding: fundamentals,
Grinding is an essential operation in cement production given that it permits to obtain fine powder which reacts quickly with water, sets in few hours and hardens over a period of weeks....The stabilisation of the cement grinding mill was studied by Grognard et al., using a state feed-back controller. The model predictive controller was designed in to Predictive Controller Design for a Cement Ball Mill Grinding
احصل على السعر
Minerals Free Full-Text Analysis and
There are usually four kinds of VRMs in the cement production line, including raw meal mill, coal mill, Clinker Mill and cement mill, and the vertical mill occupies a large energy consumption unit. This paper describes a study of the relationship between the physical, chemical and mineralogical parameters of cement products obtained by different grinding The influence of grinding technique on the liberation of
احصل على السعر
(PDF) Dust Emission Monitoring in Cement Plant Mills: A
Distribution of dust emissions at bag filters in the cement mill section no.1 (mill filterpoint A and separator filter-point B, Figure 1) of the analyzed cement plant.Based on a dynamical model of the grinding process in closed circuit mills, efficient efforts have been made to optimize PID controllers of cement milling. The process simulation is combined with an autoregressive model of the errors between the actual process values and the computed ones. Long term industrial data have been used to Optimizing the control system of cement milling: process
احصل على السعر
Investigation on grinding impact of fly ash particles and its
The cement grinding mill circuit loaded approximately 95% through clinker raw materials and rest of the feeding material is performing properties enhancer [16], [17]. In grinding process, the quality of cement in terms of fineness was measured by using Blaine's surface area and particle size distribution analysis [18] .Nowadays, ball mills are used widely in cement plants to grind clinker and gypsum to produce cement. In this work, the energy and exergy analyses of a cement ball mill (CBM) were performed andEnergy and exergy analyses for a cement ball mill of a new
احصل على السعر
Modelling cement grinding circuits ScienceDirect
Modelling and simulation studies were carried out at 26 cement clinker grinding circuits including tube mills, air separators and high pressure grinding rolls in 8 plants. March 2001 1469 1470 H. Benzer et al. Simulation of the wet grinding lines using mathematical models of the mills and separators is a technique which is being usedBesides ball mill, different types of mills which have different grinding mechanisms such as high pressure grinding rolls (HPGR), vertical mill and Horomill are being used in cement industry. Particularly HPGR has a great acceptance in cement industry for almost 20 years because of its ability to reduce specific energy consumption up to 40%.The influence of grinding technique on the liberation of
احصل على السعر
Predictive Controller Design for a Cement Ball Mill Grinding
Chemical process industries are running under severe constraints, and it is essential to maintain the end-product quality under disturbances. Maintaining the product quality in the cement grinding process in the presence of clinker heterogeneity is a challenging task. The model predictive controller (MPC) poses a viable solution to handle Section snippets Experimental work. The same lots of Portland cement clinker and natural gypsum (CaSO 4.2H 2 O) were used in this industrial-plant-scale experimental work to eliminate the potential effects of variations in the feed to the grinding systems. Chemical compositions of the clinker and the gypsum, measured by X-ray An industrial comparative study of cement clinker grinding
احصل على السعر
OPTIMIZING THE CONTROL SYSTEM OF CEMENT
Mill Feed Sep. Return Final Product System Fan Figure 1: Closed circuit grinding system. milling system is a delicate task due to the multivari-able character of the process, the elevated degree of load disturbances, the different cement types ground in the same mill, as well as the incomplete or missing information about some key process charac-Abstract The results of industrial tests of ShKh15steel grinding balls with diameters of 25, 30, and 35 mm of 5th hardness group as per GOST (State Standard) 7524–2015 at AO Kharkiv Pilot Cement Plant during grinding of cement in the second chamber of a cement mill are presented. It is shown that the use of ShKh15 steel Efficiency of Using Small Diameter Grinding Balls for Cement Grinding
احصل على السعر
Fig. 2: External view of Mill 4 (left) and mill 3
A radiotracer investigation was carried out in a ball mill of a cement plant in Kenya. Residence time distribution (RTD) of raw feed to the mill was measured using Technetium-99m adsorbed on theAbstract and Figures. Radiotracer Residence Time Distribution (RTD ) method was used to investigate the process of clinker grinding in Ghana Cement Plant (GHACEM) at Tema with the objective Radiotracer Investigation of Clinker Grinding Mills
احصل على السعر
Optimization of Feed Rate in Cement Grinding Mill Using
Approximately 95% of the feed to the cement grinding circuit are clinker and the rest of the feed are additives which includes grinding aids. The sequence of operation takes place in Cement grinding mill is as shown in figure 1. Fig. 1: Process in Cement Grinding Mill Raw materials like clinker, gypsum and fly ash areclinker to a particle size of 3...5 mm allows to exclude from the mill drum stage coarse grinding in a ball mill. Some progress got the TSG with pre-grinding cement clinker in a ball mill. One of the most economical grinding plants of this type is used in Obourg (Belgium) (Fig. 3) [15]. Mill the first stage has a size of 6×3.5 m, powerAnalysis of the efficiency of the grinding process in
احصل على السعر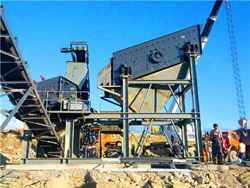
(PDF) Analysis of the efficiency of the grinding process in
Abstract. Ball mills for fine grinding cement clinker and additives are widely used around the world. To improve the efficiency of a ball grinding the ball mills are transferred in closed circuitThe cement grinding is responsible for approximately 40% of the energy consumed in a cement plant, considering an average of 110 kWh for the production of one ton of cement [4,5]. Thus, a model capable of predicting the cement fineness in real-time can improve the two indicators of the cement grinding circuit performance: energy consumptionSoft Sensor for Online Cement Fineness Predicting in
احصل على السعر
Effectiveness of triethanolamine on grindability and
The ball mill grinding process using chloride based grinding aids can be adopted at high volume replacement of fly ash in cement manufactory. [48][49], structure and hydration [12,27,50The power ingesting of a grinding process is 50-60% in the cement production power consumption. The Vertical Roller Mill (VRM) reduces the power consumption for cement grinding approximately 30-40% associated with other grinding mills. The process variables in cement grinding process using VRM are strongly nonlinear and having large time delay [PDF] PROCESS CONTROL FOR CEMENT GRINDING IN VERTICAL ROLLER MILL
احصل على السعر
Soft sensing of particle size in a grinding process:
However because of process complexity, accurate modeling of a cement mill is a difficult task. The product particle size in a cement mill is a non-linear function of the mill inputs [22]. Neural network based modeling and control strategies for product flow rate and mill load in the ball mill based cement grinding process have been developed [22].Chemical process industries are running under severe constraints, and it is essential to maintain the end-product quality under disturbances. Maintaining the product quality in the cement grinding process in the presence of clinker heterogeneity is a challenging task. The model predictive controller (MPC) poses a viable solution to handle the variability. This Predictive Controller Design for a Cement Ball Mill Grinding
احصل على السعر- production of silica ultrafine mill
- اجاره ماشین خرد کن
- آلة طحن مطحنة المملكة المتحدة
- أفضل سعر مطحنة ريموند
- material for coal hammermaterial for crusher cone
- جديدة في موردي الهند
- آلة كسارة الفحم Gujranwala
- الصين قدمت السيور الناقلة
- artificial sand making machine sale advantages of artificial sand
- محطم حلقة المحبب في محطة معالجة الفحم في
- كسارة الصخور مطحنة المطرقة الصغيرة للمنقبين أستراليا
- 600 tph 8211800 tph كسارة الحجر
- chines feed mill beautiful boundary wall
- مباشرة سائق محطم كسارة الدوران
- مطحنة Amp3bamp تعدين الفحم تعدين