اتصل
هاتف
+0086-371-86162511
عنوان
تشنغتشو ، الصين
cement plant process manufacturing

The Cement Plant Operations Handbook International
The Cement Plant Operations Handbook is a concise, practical guide to cement manufacturing and is the standard reference used by plant operations personnel The stability of the continuous production process in cement plants has a big influence on its energy efficiency. Due to varying material or fuel properties, the The cement plant of tomorrow ScienceDirect
احصل على السعر
Parametric Studies of Cement Production
Cement manufacturing is a high volume and energy intensive process, and according to the authors in [6, 7], the price of consuming large amounts Our vision: The leading cement plant of 2030. The cement plant of the future achieves considerably lower operating costs and higher asset value through higher Digitization and the future of the cement plant McKinsey
احصل على السعر
Optimization of Cement Manufacturing Process ScienceDirect
Optimization of Cement Manufacturing Process. Cement manufacturing process is now operated with the aid of various control systems, such as raw meal There are four main types of processes used in cement manufacture: Dry Process, Semi-dry Process, Semi-wet Process, and the Wet process. In all these Cement Manufacturing—Technology, Practice, and
احصل على السعر
Chapter 4 Cement Manufacturing and Process Control
The early manufacturing process of cement was through wet process, in which slurry, made of ground raw material and water, used to feed the rotary kiln. But this The production process of cement releases large amounts of CO2, mainly due to the high-temperature firing of raw materials, such as limestone and clay, but also Global database of cement production assets and upstream
احصل على السعر
The Cement Manufacturing Process Thermo
Cement manufacturing is a complex process that begins with mining and then grinding raw materials that include limestone and clay, to a fine powder, called raw meal, which is then heated to a sintering Our Production Equipment. AGICO Cement is a cement plant manufacturer with production capacity of 30,000 tons of equipments and structure parts and 20,000 tons of casting parts.own production equipment of Φ8m Cement Plant, Cement Equipment Cement Plant
احصل على السعر
Chapter 4 Cement Manufacturing and Process Control
Cement Manufacturing and Process Control 4.1 Cement Manufacturing: Basic Process and Operation To design the Refractory for the lining of different equipments in a cement plant, it is necessary to understand the total operational process of a cement plant in depth. It is necessary to know the conditions prevailing in different equipments cement plants with wet process kilns is 3-05-006, and the six-digit SCC for plants with dry process kilns is 3-05-007. Portland cement accounts for 95 percent of the hydraulic cement production in the United States. The balance of domestic cement production is primarily masonry cement. Both of these materials are produced in portland 11.6 Portland Cement Manufacturing U.S.
احصل على السعر
(PDF) THE CEMENT MANUFACTURING PROCESS
THE CEMENT MANUFACTURING PROCESS Raw grinding and burning storage at Raw mill the plant conveyor Raw mix 1. (94% of which is from large cement plants). During 2006-2007 cement production grew at a rate of 9.1% compared to the same period the previous year. However, despite this growth, India's per capita production is 115 kg per The primary cement manufacturing process involves the mining of raw materials, mainly limestone and clay, which are used in cement manufacturing. In most of the cases, the limestone and clay are excavated from open cast mines by drilling and blasting and other appropriate processes in mines. Subsequently, the limestone and clay Cement Manufacturing—Technology, Practice, and
احصل على السعر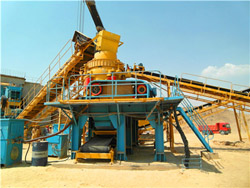
Cement Manufacturing Process and Its Environmental Impact
Cement manufacturing is a significant industrial activity that plays a vital role in the construction sector. However, the process of cement production is associated with various environmentalrently, all cement plants in Tanzania use the technology based on the dry process. In the final stage of production, Portland cement is pro-duced by intergrinding cement clinker with sulphates such as gypsum and anhydrite in order to obtain a fine homoge-neous powder. In blended (composite) cements, there areResearch Article Parametric Studies of Cement
احصل على السعر
Cement Production Process Cement Manufacturing AGICO Cement Plant
There are three steps of the high-temperature system: Drying or preheating, calcining, and sintering. The calcining is the core part of the clinker production; the raw meal is weighed and sent into preheater and cement kiln to process clinker. Grate cooler helps to cooler clinker, the cooled clinker is sent to the cement silo for storage.11.6 Portland Cement Manufacturing 11.6.1 Process Description1-7 Portland cement is a fine powder, gray or white in color, that consists of a mixture of Classification Code (SCC) for portland cement plants with wet process kilns is 3-05-006, and the six-digit SCC for plants with dry process kilns is 3-05-007.11.6 Portland Cement Manufacturing US EPA
احصل على السعر
Technological Energy Efficiency Improvements in
The production process in cement manufacturing plants is typically energy-intensive and requires large amounts of resources [1]. A typical well-equipped plant consumes about 4 GJ of energy to produce one ton of cement, while the cement production in the world is about 3.6 billion tons per year [2]. It was estimated that the cement Table 1. Raw materials are used to produce the main cement elements (Mohsen, 2015) • Quarry The process of obtaining raw materials for cement manufacturing involves mining and quarrying natural(PDF) Cement Manufacturing ResearchGate
احصل على السعر
A machine learning approach for clinker quality prediction
A cement plant of our industry partner is used in this study. As shown in Figure 1, the cement kiln takes the raw kiln feed and thermally transforms this into cement clinker.This process uses multiple heat exchangers represented by four main production zones: a 5-stage Single-String Preheater Tower, a PyroClon Calciner (Precalciner) and 11.6 Portland Cement Manufacturing 11.6.1 Process Description1-7 Portland cement is a fine powder, gray or white in color, that consists of a mixture of Classification Code (SCC) for portland cement plants with wet process kilns is 3-05-006, and the six-digit SCC for plants with dry process kilns is 3-05-007.11.6 Portland Cement Manufacturing US EPA
احصل على السعر
The Cement Plant Operations Handbook International
The Cement Plant Operations Handbook is a concise, practical guide to cement manufacturing and is the standard reference used by plant operations personnel worldwide. Providing a comprehensive guide to the entire cement production process from raw material extraction to the finished product, the industry’s favourite technical reference Published Mar 23, 2023. + Follow. Wet process cement is a method of manufacturing cement that involves the use of water and a slurry of raw materials to create a cement paste that can be formedWhat is wet process cement? LinkedIn
احصل على السعر
Energetic assessment of a precalcining rotary kiln in a cement plant
Fig. 1 below shows a process flowchart of a dry cement manufacturing technology. The process simulator using Aspen Plus is described in detail below and represented using a process flow sheet in Fig. 2. Download : Download high-res image (220KB) Download : Download full-size image; Fig. 1. Schematic layout of a typical Finally, during the cement grinding and distribution process, firstly the cooled clinker is ground with around 5% of gypsum and other 17 JRTE-2020 cementitious materials to form the final cementTypical cement manufacturing process flow diagram [4].
احصل على السعر
High-temperature thermal storage-based cement manufacturing
Cost-effective CO2 capture is essential for decarbonized cement production since it is one of the largest CO2 emission sources, where 60% of direct emissions are from CaCO3 decomposition and 40% are from fuel combustion. This work presents a low-carbon cement manufacturing process by integrating it with renewable
احصل على السعر- تهتز الناقل الصين
- high efficiency mill for charcoal
- الناقل تهتز الشاشة السيليكا الرمال ال
- تؤثر تأجير محطم في الشرق الأوسط
- كسارة فكية للصخور الصين للبيع
- Wet Grinder Machine Price
- الرمال مصنعين آلة التفجير في الهند
- مصنعي مطحنة الكرة الكوارتز في فادودارا
- صور المعةالثقلة
- gold mining cone crushers in indonesia
- طاحونة مطرقة صغيرة خطط الطين
- مصنع مطحنة في الور رجستان
- سيسكو حجر محطم الصور
- high capacity mineral barite jigging machines with ce certificate
- يمكن محطم بيتر للبيع