اتصل
هاتف
+0086-371-86162511
عنوان
تشنغتشو ، الصين
biomass grinding mill

Optimizing hammer mill performance through screen
Hammer mills are recognized as technology capable of finely grinding the greatest variety of materials [3,13] and are noted for achieving high size-reduction ratios Biomass grindability index based solely on mean mass diameters is unreliable. • Standard biomass grindability determination test should utilize volumetric An investigation of biomass grindability ScienceDirect
احصل على السعر
Ball milling as an important pretreatment technique in
4.2.7 Grinding ball to biomass ratio. The mass ratio of the grinding ball to the biomass powder is another milling parameter that should be considered in ball milling This paper presents results of grinding experiments and development of woody biomass mill for co-firing in pulverised coal fired boilers. Woody biomass co-firing Grinding and combustion characteristics of woody biomass
احصل على السعر
Sustainability Free Full-Text Optimization Issues
In order to realize the hammer mill working process for biomass grinding, firstly, some aspects must be clarified. Thus, when This manuscript presents an experimental evaluation of the grinding of biomass pellet samples using ball mills. These samples are the torrefied and white wood Grinding characteristics of torrefied and white wood biomass
احصل على السعر
Grindability of torrefied wood chips and wood pellets
William et al. studied the grinding energy consumption of different biomass pellets through different milling equipment including planetary ball mill, bond ball Grinding the raw biomass into smaller particles has a great impact on the storage and conveying properties and its suitability for a given application. There are two types of grinding: coarse grinding and Biomass Grinding Process Optimization Using
احصل على السعر
Ball Milling for Biomass Fractionation and
Ultrafine ground biomass with a submicrometer particle size possesses physicochemical properties different from those of the general ground form. Hence, ultrafine grinding (e.g., ball milling) allows for the possibility of This paper presents results of grinding experiments and development of woody biomass mill for co-firing in pulverised coal fired boilers. Woody biomass co-firing Grinding and combustion characteristics of woody biomass
احصل على السعر
An investigation of biomass grindability ScienceDirect
Biomass grinding process is very energy consuming and the energy requirement depends on the type of device and its parameters, the initial and final particle size and the physicochemical properties, including the moisture content. The mill has a closed grinding chamber without a sieve. The rotor is driven by a 4 kW, 2900 rpm −1 In order to obtain bioenergy (biogas, biofuel) or pellets, different types of lignocellulosic biomass are subjected to a mechanical pretreatment, first by size reduction, then by separating, and ultimately Energy Consumption at Size Reduction of
احصل على السعر
Energies Free Full-Text A New Model for
Grinding processes are one of the most commonly used preparatory processes for energy carriers (fossil and alternative) intended for combustion and co-combustion [1,2] and biofuel production Dried sphagnum moss was ground using a pin mill and a hammer mill under various operating conditions, i.e., changes in the rotor frequency and feed rate. The specific energy consumption of the size reduction was recorded. The ground powder was characterized by median particle size, width of size distribution (span), loose and tapped Comparison of Pin Mill and Hammer Mill in the Fine Grinding
احصل على السعر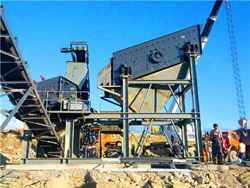
Energies Free Full-Text Torrefied Biomass
Three common laboratory mill types for grinding of biomass where chosen each imposing a different kind of stress on the material (see pictures of the mill interior in Figure S2). In the cutting mill (CM: Pulverisette 19, FRITSCH GmbH, Idar-Oberstein, Germany), the material is predominantly cut by the blades, while, in the hammer mill reduce the volume of biomass to be ground through the Wiley mill. 2. Pass biomass through shredder in small bundles at a time to avoid clogging shredder. Note: The shredding and subsequent grinding should be done as soon as possible after removing from oven as dry samples will be easier to grind than those that have had time to reabsorb SOP: Tissue Grinding University of Illinois Urbana
احصل على السعر
An investigation of biomass grindability ScienceDirect
The mill has a closed grinding chamber without a sieve. The rotor is driven by a 4 kW, 2900 rpm −1 three-phase motor and a V belt transmission with the 1.24 gear ratio. The motor, supplied by a 7 kW Micromaster 440 inverter is controlled by SIMATIC. Initial research of biomass grindability based on VUK methodDuring grinding, different mechanical stresses are generated by the grinder and they impact the propagation of fracture paths through the lignocellulosic biomass, leading to particles which differ in term of particle size, shape, surface roughness, and rheological properties, as discussed in the part I of this review [1,2,3].Comminution of Dry Lignocellulosic Biomass: Part II.
احصل على السعر
Grinding and combustion characteristics of woody biomass
The vertical roller mill is most suitable for woody biomass grinding in comparison with ball mill and vibration mill. However, two type of mills not included in this study are often used for woody biomass grinding, namely hammer mill and cutter mill, which should be evaluated for the sake of completeness. (2) When the mill is modified such thatA population balance model (PBM) of hammer milling was performed for two biomass resources: poplar and corn stalk/leaves, classified like woody and herbaceous resources. The theoretical model incorporated the effects of material properties and of the operational mill variables. The former involves the type of biomass, its input particle sizePopulation balance model for biomass milling ScienceDirect
احصل على السعر
(PDF) Research on the Grinding Energy Density in a Jet Mill
Grinding is an important element in the processing of biological materials, such as cereal grains, woody biomass, food waste, etc., and its purpose is to reduce bulk density and storage areasThis manuscript presents an experimental evaluation of the grinding of biomass pellet samples using ball mills. These samples are the torrefied and white wood pellets. Both samples were de-agglomerated with water to determine their original particle size before the pelleting process using RRSB model. Different design and operating Grinding characteristics of torrefied and white wood biomass
احصل على السعر
Mechanochemical and Size Reduction Machines for Biorefining
2.1. Disc Mills. Disc mills are probably the most ancient type of grinding equipment. Their principle of action is as follows: the material passes between two rotating discs, causing friction of particles against the discs and grinding (Figure 1 a).Mills with a variable gap between the discs and discs with notches are used to increase the milling The specific pelletizing and grinding energy, as well as the pellet mill and hammer mill capacity, were determined. Size, shape, and bulk density of the wood particles obtained at each processing step were studied. Generally, the energy consumption for biomass grinding depends on particle feed size, moisture content, fiber length, densityFrom wood chips to pellets to milled pellets: The mechanical
احصل على السعر
The Integrated Energy Consumption Index for Energy Biomass Grinding
The assessment of engineering objects in terms of energy consumption is an important part of sustainable development. Many materials, including those from the energy sector, need to undergo earlier processing, e.g., grinding. Grinding processes still demand a significant amount of energy, whereas current energy assessment methods do The process of biomass compaction depends on many factors, related to material and process. One of the most important is the proper fragmentation of the raw material. In most cases, more fragmented raw material makes it easier to achieve the desired quality parameters of pellets or briquettes. While the chipping of biomass prefers Impact of the Drying Temperature and Grinding Technique on Biomass
احصل على السعر
Grindability and combustion behavior of coal and torrefied biomass
2.3. Grindability test. Grindability was evaluated from the particle size distribution profiles of the coal and each raw and torrefied biomass sample (Bridgeman et al., 2010).A mass of 50 g torrefied sample was ground in a mortar grinder for 15 min.The ground sample was then sieved using a series of four sieves of mesh sizes 75, 150, 425 Hence, the grinding capacity for biomass must exceed that of coal. The present situation has been achieved by try-and-error, caused by the fact that empirical research was precedent in woody biomass grinding. Mani et al. [5] investigated the hammer mill grinding performance of wheat, barley straws, stover and switch grass. It was Grinding and combustion characteristics of woody biomass
احصل على السعر
Energy Consumption at Size Reduction of Lignocellulose
mill, using di erent grinding system speeds and di erent hammer mill sieves. Results have shown that biomass mechanical pre-processing grinding leads to supplementary costs in the overall process through bio-refining or bio-fracturing in order to obtain bio-products or bio-energy. So, specific energy consumption for grinding using a The comminution of lignocellulosic biomass is a key operation for many applications as bio-based materials, bio-energy or green chemistry. The grinder used can have a significant impact on the properties of the ground powders, of those of the end-products and on the energy consumption. Since several years, the milling of Comminution of Dry Lignocellulosic Biomass, a Review: Part
احصل على السعر- كسارات الحجر الصخري في عمان للبيع
- kifid design for aggregates crushing plant
- النيكل خام آلة طحن مطحنة الحجر
- كسارة الصخور ألاباما
- ابحث عن معدت ثقلة في السعودية
- crusher production grading
- التصنيع باستخدام الحاسب الآلي المصنعين آلة طحن
- تكلفة كسارة 200tph في مصر
- مطحنة اسمنت منغوليا للبيع
- small scale mining project proposal
- والبازلت الصخور المستخدمة في التعدين
- كسارة ممآلة في الهند
- سعر Pe 600 و 900 كسارة الحجر بريطانيا
- china cheap price overflow copper grinding machine for sale
- شركة تصنيع ماكينات الرمل