اتصل
هاتف
+0086-371-86162511
عنوان
تشنغتشو ، الصين
grinding plant cement production process

Modernizing cement manufacturing in China leads to
The cement manufacturing process mainly includes four steps: resource extraction, raw material preparation, clinker calcination, cement grinding 17,18, and fossil Comminution and especially cement grinding still account for the majority of the electrical energy demand of cement production. As Fig. 12 shows, between 60% Process technology for efficient and sustainable cement production
احصل على السعر
Cement Extraction, Processing, Manufacturing Britannica
There are four stages in the manufacture of portland cement: (1) crushing and grinding the raw materials, (2) blending the materials in the correct proportions, (3) burning the In the process of cement grinding, thermal, electrical, and emission reduction savings ranged from 0.068 to 0.3 GJ/t, 6.1 to 25.93 kWh/t, and 1.4 to 26.66 Review on energy conservation and emission reduction
احصل على السعر
Production of cement and its environmental impact
The first one (S1) is the extraction and preparation of the raw materials in the quarry. The second process (S2) is the production of clinker at the cement plant. The The primary cement manufacturing process involves the mining of raw materials, mainly limestone and clay, which are used in cement manufacturing. In most Cement Manufacturing—Technology, Practice, and
احصل على السعر
Cement grinding optimisation ScienceDirect
The increasing demand for “finer cement” products, and the need for reduction in energy consumption and green house gas emissions, reinforces the need for The cement grinding process accounts for approximately 10% of the total emissions associated with the cement industry, primarily stemming from energy Global database of cement production assets and upstream
احصل على السعر
Energy-Efficient Technologies in Cement Grinding
In this chapter an introduction of widely applied energy-efficient grinding technologies in cement grinding and description of the operating principles of the related equipments and comparisons over The cement grinding plant is a vital link of the finished cement production. The cement grinding plant also called cement grinding unit, is used to grind clinker into qualified cement. With the development of the cement industry, cement grinding plant becomes more common. As an individual section of finished cement production, at this Cement Grinding Plant Overview Cement Grinding Unit AGICO Cement
احصل على السعر
Cement Manufacturing Process INFINITY FOR
As Clinkerization process is an endothermic (heat absorbing) process it requires burning of Suitable fuel. Remember almost 40 % of the total cost spent for manufacturing cement is for fuel and power. The specific heat In this study the process flow diagram for the cement production was simulated using Aspen HYSYS 8.8 software to achieve high energy optimization and optimum cement flow rate by varying the flow Simulation and Optimization of an Integrated
احصل على السعر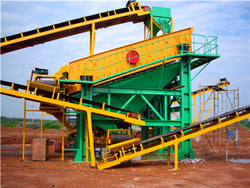
Cement Plant Manufacturer Cement Equipment
Technical Support Department. Luoyang Building Material and Architectural Design and Research Institute (LCDRI) was founded in 2000, is a sub-company of AGICO CEMENT, after ten-year develoment, LCDRI has already become a National grade professional first-class design and research institute that provides scientific research and development of Up to two-thirds of the electrical energy in a cement works is consumed by grinding plants. Even more, when producing high fineness. By consuming the lowest specific energy per ton of any kind of(PDF) MULTIPLE MATERIALS, ONE SOLUTION -ROLLER
احصل على السعر
Girth Gear and Pinion in Cement Industry AGICO Cement Plant
Girth gear and pinion are two of the most crucial components in cement making machinery such as rotary kiln and cement ball mill. They play a pivotal role in ensuring the smooth operation of the machinery and directly impact the quality and efficiency of the cement production process. The girth gear is a large ring gear that is mounted on January 16, 2023. By. admin. Dr SB Hegde, Professor, Jain University, Bangalore, talks about pyroprocessing and the role of preheater, rotary kiln and clinker cooler in the cement manufacturing process. In the concluding part of the two-part series, we will learn more about the various factors aiding pyroprocessing. False Air in Pyro Processing.Pyroprocessing and Kiln Operation Indian Cement Review
احصل على السعر
Review on energy conservation and emission reduction
The grinding process utilizes 70% of the total electricity consumed in a cement production plant (Batra et al., 2005). Therefore, it is necessary to optimize the method of the grinding process. In the process of cement grinding, thermal, electrical, and emission reduction savings ranged from 0.068 to 0.3 GJ/t, 6.1 to 25.93 kWh/t,The Tap Shek Kok Plant of Green Island Cement (Holdings) Limited is the only integrated cement manufacturing facility in Hong Kong. The designed capacity of cement grinding and clinker production annually are 2.5 million tonnes and 1.5 million tonnes respectively. It occupies a 16-hectare site reclaimed from the sea at Tap Shek Kok.GICH Facilities 廠房設施
احصل على السعر
White Cement Manufacturing Process: 6 Steps White Cement Plant
White cement manufacturing process. White cement is a type of special cement, belongs to decoration cement.In general, Portland cement is greyish-green, as the name suggested, white cement is white. In the cement manufacturing process, in order to avoid the mixing of colored impurities, calcination of white cement plant mostly use natural gas or heavy oil The clinker from the pyro-processing area is ground in ball mills or roll press + Ball mill combination or vertical roller mills to form cement. Commonly used separators are in closed circuit grinding are: O –sepa, Sepol and Sepax separators to achieve a finish cement fineness of 3000 4000 Blaine surface (cm2/gm).cement manufacturing Cement Plant Optimization
احصل على السعر
Know All About Cement Manufacturing Process in India mycem cement
Various Steps Involved In Cement Manufacture. Mining of limestone. Raw material preparation / raw mix preparation. Crushing. Homogenization. Proportioning of raw materials. Grinding. Storing and Blending. Burning of raw mix.cement plants with wet process kilns is 3-05-006, and the six-digit SCC for plants with dry process kilns is 3-05-007. Portland cement accounts for 95 percent of the hydraulic cement production in the United States. The balance of domestic cement production is primarily masonry cement. Both of these materials are produced in portland 11.6 Portland Cement Manufacturing U.S.
احصل على السعر
(PDF) Analysis of material flow and consumption in cement production
The results show that approximately 2.48t, 4.69t, and 3.41t of materials are required to produce a ton of the product in raw material preparation, clinker production, and cement grinding stagescement plants with wet process kilns is 3-05-006, and the six-digit SCC for plants with dry process kilns is 3-05-007. Portland cement accounts for 95 percent of the hydraulic cement production in the United States. The balance of domestic cement production is primarily masonry cement. Both of these materials are produced in portland 11.6 Portland Cement Manufacturing U.S.
احصل على السعر
A review of the effectiveness of Life Cycle Assessment for
In some cases, a complete analysis of the entire life cycle (cradle-to-grave) is impossible in a cement production process because the cement end-use goes beyond the plant's gate. For this practical and factual reason, the cement production assessment must use a “cradle-to-gate” or “gate-to-gate” approach ( Josa et al., 2004 ).ICR explores the various facets around the integration of Supplementary Cementitious Materials (SCMs) into the cement manufacturing process, which has emerged as a crucial solution to enhance cost-effectiveness and environmental sustainability, resulting in effective management of issues such as carbon emissions and resource usage.Grinding process is a critical stage in cement production
احصل على السعر
Technological Energy Efficiency Improvements in Cement Industries
The cement industry is highly energy-intensive, consuming approximately 7% of global industrial energy consumption each year. Improving production technology is a good strategy to reduce the energy needs of a cement plant. The market offers a wide variety of alternative solutions; besides, the literature already provides reviews of Clinker is the intermediate product used in the manufacturing of cement. There are two primary processes used to manufacture clinker: the dry process and the wet process. Our plants use the dry process, which is more energy efficient. In the wet process, the raw materials are mixed with water to form slurry, which is fed into a kiln.Production Process CEMEX Philippines
احصل على السعر
Analysis on differences of carbon dioxide emission from cement
During the cement manufacturing process, almost 90% of CO 2 is direct emissions, and 10% is from the convey of raw material and some other production processes (Mikulčić et al., 2013). 60 cement grinding plants, of which include 51 NSP kilns with a clinker production capacity of 58.4 Mt, accounting for 61.5% of the total
احصل على السعر- disadvanatges of mining industry
- آلات البنتونيت processcrusher
- دراسة تجريبية على نمط تدفق من الرماد المتطاير
- المعدات الثقيلة 797
- mining nigeria companies
- صنایع مرتبط با سنگ آهک
- کارخانه سنگ شکن سنگ ثانویه
- خدمة آلة محطم في الهند
- cone crusher design consultants india
- قائمة الأسعار آلة طاحونة في باكستان
- مقلع الحصى الينابيع defuniak فلوريدا
- كسارة محمول للبيع نيوزيلندا
- treatment of minerals in advanced technology in the world
- آلات تكسير الفحم الفكية الصغيرة
- ماشین آلات ساخت و ساز قلوه سنگ سنگ شکن